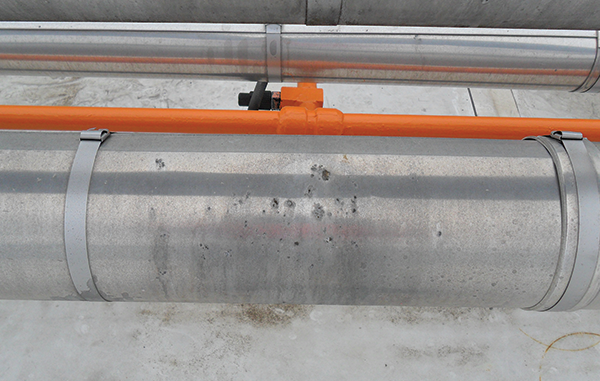
Originally published by NIA Copyright 2019. Reprinted with permission from Insulation Outlook magazine, a publication of the National Insulation Association (www.Insulation.org).
By / par Ron King • Photos / Jim Young
The many aspects of corrosion under insulation (CUI) have been debated for years. Does mechanical insulation cause corrosion or help prevent corrosion, or is it just an innocent bystander in the debate? I am by no means a corrosion specialist or an insulation technical guru, but I do take a practical approach to addressing the primary question. This article will explore the practical aspects of the debate and, depending on your point of view, contribute to the debate. I am convinced the debate will not be resolved with this article, but I hope it will make you think about insulation differently when examining CUI.
Corrosion under insulation can be extremely bad because it is often hidden. When it becomes noticeable, the consequences are usually bad and potentially unexpected. When I hear someone indicate the problem was unexpected, I really don’t understand their comment. It reminds me of the old saying: “out of sight, out of mind.” It may not have been expected at that time, but it was going to happen sooner or later unless steps were taken to prevent or minimize the danger.
The damage created by CUI was being debated as early as the 1950s. The magnitude of the overall corrosion issue has been reported to cost industry billions of dollars annually. How much is directly attributable to CUI is part of the debate. The growth rate of the overall problem and CUI is also widely disputed. But with today’s emphasis on short-term cost abatement or deferral, I would not be surprised if a spike appears.
Where Can CUI Occur and Why?
The short answer is everywhere. The two most commonly discussed substrates are carbon steel and austenitic stainless steel. The carbon steel corrodes or rusts, and the stainless steel cracks. They don’t crack or corrode because they are insulated but because they have come in contact with moisture. Insulation does not cause corrosion.
For CUI to form on carbon steel type surfaces, they must be exposed to oxygen, moisture, and warm temperatures. For austenitic stainless steel type surfaces, chlorides or similar type halides must also be present at the substrate. The rate of corrosion or cracking will depend on any combination of these factors.
Insulation provides an annular space where moisture can be retained. Depending on the source of the moisture, it could contain other contaminants. Could that accelerate the rate of corrosion? Yes. Can some insulation in the presence of water contribute additional contaminants that could cause or accelerate corrosion? Yes. Could some insulation “wick” or absorb moisture faster or to a greater extent than others? Yes. The common denominator in all three scenarios is insulation in the presence of water.
CUI is not limited to pipe and equipment walls but can also affect instruments, tubing, valves, bolts, and many other areas that could interfere with facility operations. CUI left unattended can also foster and accelerate the failure of an insulation system through weakening the substrate, cracking the insulation system, and causing leaks.
Service Temperature versus CUI
From all I have read, carbon steel operating in the temperature range of 25°F to 300°F is at the greatest risk of CUI. Surfaces that operate below 25°F seem to be usually free of CUI, and those operating above 300°F usually have reduced rates of CUI. However, those temperature parameters are only rough guidelines. I have seen CUI at the point of moisture intrusion, at water/ice transition areas, and especially in cyclical service situations and when piping and equipment are idle. Cyclical service and start up from an idle mode can create many problems if moisture is in the insulation system.
Stress cracking of austenitic stainless steel occurs when chlorides in the environment or insulation material are transported by water to hot surfaces and concentrated by evaporation of the water. Insulation can provide the vehicle to transport those chlorides to the surface. Over time, the concentration of those contaminants can escalate the problem.
What are the Potential Sources of Moisture Intrusion in an Insulation System?
There are multiple sources, not in any particular order of importance or frequency of occurrence:
- Rainwater
- Wash down process
- Water vapor penetrating the insulation system
- Ice formation and potential freeze-thaw situations
- Fire detection system activation
- Equipment or piping leaks
- Flooding
There are many kinds of opportunities for moisture to enter an insulation system. Many experts have indicated that moisture entering an insulation system is not a question of if, but when and how much. They may be correct, but I believe the risk of CUI can be managed by understanding the risks of allowing moisture intrusion and correcting damage in a timely manner.
Insulation System Design
Prevention of CUI begins with the facility design and extends through the design and installation of the mechanical insulation system. A poorly designed and installed insulation system that allows moisture intrusion is problematic for many reasons.
One of the most common areas of concern is penetrations. In many cases, the design of the mechanical system does not give adequate consideration to the complexity and difficulty of insulating or sealing and maintaining the integrity of that seal.
Another design flaw often occurs in the selection of a protective and/or vapor/moisture barrier for the insulation system. The characteristics of the core insulation material are important, but the selection of the vapor barrier and protective coating or jacket appropriate for the service temperature and environment is critical.
Take the time to thoroughly investigate the insulation system options and take a “real world” approach to actual field conditions and maintenance expectations. Seek advice; this is too important not to avail yourself of every opportunity to get it right. Attempts to prevent water from entering an insulation system over time have been less than successful for a variety of reasons. In addition, corrosion protective techniques in many cases have not been effective. Realize that moisture is the primary enemy and you have identified the real problem: controlling and/or eliminating moisture intrusion.
The Importance of a Proper Insulation Maintenance Program
One of the problems is that insulation systems are not being maintained in a timely and proper manner. This is why 10 to 30 percent of installed mechanical insulation systems are damaged or missing within a few years of initial installation. That is a recipe for CUI.
You should maintain an insulation system in a timely and correct manner for a number of reasons:
- Safety
- Corrosion of the substrate under the insulation (CUI) could result in product release.
- The increased weight of wet insulation and/or ice, depending on the service and ambient conditions, could cause the piping or equipment to exceed the structural design of the support hangers or other support systems.
- Continual dripping of water from insulation and/or melting of the ice that has formed on and in an insulation system could create a personnel safety concern.
- Plant Environment and Regulations
- Wet insulation and increased presence of water from the melting ice or dripping from insulation can contribute to the development of mold on and in the insulation system and in adjacent areas.
- Energy Loss and Greenhouse Gas Emissions
- While wet insulation and ice do have some minor insulation value, the additional heat gain from the failed insulation systems will result in increased energy consumption and greenhouse gas emissions.
- Productivity
- The reduced efficiency of the insulation system does not allow the process equipment to function as designed, resulting in decreased productivity and/or increased cost of production.
- Cost of Operations/Return on Investment
- A failed insulation system increases annual operating cost and lifecycle cost through:
- Increased energy consumption and cost
- Increased production cost and lower throughput
- Decreased life of the substrate, which increases life cycle and annual maintenance cost in multiple areas
- Deceased life of equipment due to operational demands and the effect on the surrounding work area
- Unnecessary risk in areas including employee and community safety and regulatory concerns.
- A failed insulation system increases annual operating cost and lifecycle cost through:
Another recipe for CUI is failure to immediately and properly repair an insulation system after non-destructive testing. Many non-destructive testing procedures should be described as “destructive.” Any time an insulation system is penetrated, the integrity of the overall system is compromised. This is especially true on services below ambient temperatures. The problem is compounded when the area penetrated is not properly repaired in a timely manner.
Non-destructive testing is a double-edged sword. CUI can be hard to detect unless you inspect the substrate regularly, but if the inspection process has flaws, like not immediately repairing the insulation, it can cause or compound problems.
Inconsistent levels of effective and timely maintenance of insulation systems can only lead to increased CUI concerns and intensity of the problem. Would a consistent, proper, and aggressive insulation system maintenance program eliminate CUI? Total elimination of the problem is not a realistic assessment, but such a program would substantially reduce the extent and severity of the problem.
The Bottom Line
CUI costs industry billions of dollars annually, yet many companies do not address the real problem of proper design, installation, and maintenance of mechanical insulation systems. That is why I am surprised when I hear someone indicate the problem was unexpected. If you don’t have the proper design, proper installation, and a timely and effective insulation maintenance program, why should you be surprised when CUI is finally recognized? With CUI, examining the long-term cost and benefits can save a great deal of money over time.
Spending time in the design of insulation system, ensuring it is properly installed by an experienced and proven insulation contractor, and implementing a timely, effective maintenance program are necessary to prevent CUI. The benefits of such a process will exceed your expectations. In today’s economy, it has never been more important to think about insulation and corrosion under insulation differently.
May 2019 Update: 10 Years Later
This article was originally published in June 2009. When asked if it could be reprinted in May 2019, my first reaction was that a lot has changed in 10 years. However, after reviewing the article, I found the message remains valid and the debate continues.
Insulation does not cause corrosion. The temperature range where corrosion can occur may vary depending upon who is asked, but it still takes three items to create CUI:
- temperature
- prolonged exposure to moisture
- water and containments (which can be from the atmosphere, water, or from the insulation in the presence of water).
Many believe that water or water vapor will eventually find its way into an insulation system. If that is the case, and if the water cannot find its way out and remains within the insulation at the substrate level, the risk of developing corrosion is high. Contaminated water reaching the substrate is not the problem, the retention of water or continual exposure to contaminated water at the substrate is the problem.
Inspection of mechanical insulation can play a vital role in helping to identify potential areas where CUI can occur and areas in need of repair of replacement before CUI becomes a major problem that could lead to significant financial loss, personal injury, or even loss of life.
Today, when you hear others talk about CUI and insulation materials you will hear phrases like water resistant, corrosion inhibitors, hydrophobic, and hygroscopic.
- Water resistant means basically the material is able to resist the penetration of water to some degree, but not entirely unless it and the system is zero perm.
- Corrosion inhibitors are combined with the material to reduce the rate at which corrosion on the outer surfaces of pipe and equipment may occur.
- Hydrophobic means the material tends to repel or not to absorb water.
- Hygroscopic refers to the material’s ability to absorb and hold water.
Virtually every material has limitations. As an example, some materials may lose their hydrophobic qualities at certain temperatures or upon other occurrences. They are currently no insulation “silver bullets” to prevent CUI. When it comes to minimizing CUI, a total system design approach, substrate preparation and coating, and all aspects of an insulation system, is required and a proactive inspection and maintenance program is needed.
Now you know a little bit about CUI, but I am sure the debate will continue.
Ronald L. King
Ron King is a Past President, and Honorary Member, of the National Insulation Association (NIA), the World Insulation and Acoustic Organization and the Southwest Insulation Contractors Association. He was awarded the NIA’s President’s Award in 1986 and again in 2001. He is a 50-year veteran of the commercial and industrial insulation industry, during which time he held executive management positions at an accessory manufacturer and specialty insulation contractor. He can be reached at 281-360-3438 or RonKingRLK@aol.com.