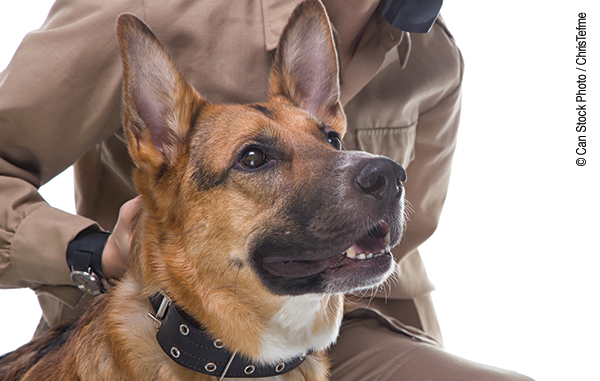
A two-year project carried out by the Fjellanger Detection and Training Academy (FDTA) in Norway, funded by Gassco, and supported by Norwegian energy giant Equinor (previously Statoil), investigated the use of remote scent tracing (RST) technology—a system where the volatile elements associated corrosion are sampled and detected using the sensitive nose of a trained canine—to detect corrosion under insulation (CUI).
Dogs used as detectors in RST technology usually detect the presence of explosives or contraband in scent samples collected by sucking air from containers or air freight. In this study, five dogs were trained to detect CUI of pipes in scent samples collected at a gas processing plants. The onus for the study was the major cost problem CUI causes oil and gas processing plants and other industrial and commercial applications. CUI causes safety risks, time and costs lost, and production downtime.
Scent samples of the elements associated with corrosion were created by sucking air through drain plugs in the insulation material surrounding the pipes onto filters. From 2015-2017, dogs were trained to detect corrosion using insulation material collected earlier from other corroded locations at the plant and were able to detect corrosion on the filters collected from intact insulated pipes at that plant at consistent proficiency, detecting corrosion at around 59% while producing on average less than 3% false alarms.
RST technology comprises two steps—sampling the item or element onsite and analysis offsite involving dogs and the FDTA. In this study, the dogs were able to discriminate between field samples collected near corroded pipes and samples collected from non-corroded locations equally well as they discriminated between training samples.
A number of locations were tested double blind: a situation where no one at the time of sampling or analysis by the dogs knew if the location was corroded or not. Locations that the dogs responded to were opened later for a general visual inspection, and corrosion was found under the insulation. No corrosion was found at locations that the dogs had not responded to.
A system approach was chosen where the response of a number of dogs was combined. In this manner, areas that were analyzed could be divided into high, low, or no suspicion of corrosion. The result of the project was that the system is now a proven technology and is ready to be integrated into plant maintenance systems.
Preliminary results on double blind samples were promising: the sensitivity of the detection of field samples was 92%, and the selectivity 93%. The application of such a system as a tool in a preventive maintenance program at oil and gas processing plants could be useful to determine timing of maintenance, thus allowing a more efficient allocation of costly resources necessary for the customary visual inspection.
To learn more, please see the resources in the box below.