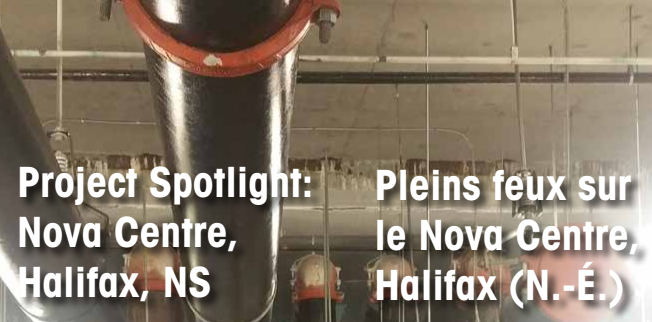
Mechanical insulation on the 100 per cent design-build project was supplied by Scotia Insulations and installed by Pro Insulation Ltd. Robert Knox, sales representative for Scotia Insulations, said the convention centre, hotel, and office towers were phased to meet the building schedule.
The insulation scope includes all the ventilation, the HVAC system, and all mechanical plumbing and heating systems. The team used standard insulation types including fiberglass, ASJ pipe insulation, fiberglass rigid board, duct wrap, and pipe and tank wrap, as well as dry grease and duct insulation for the commercial kitchen component.
“This is a different type of project because it is one of the largest commercial projects east of Toronto, and it is actually being developed by a private developer for the government of Nova Scotia,” said Knox. “The government plans to lease the building for a number of years and then have the option to buy it.”
The project challenges began with three storeys below grade and one tower reaching 21 storeys in total—a design that required intense planning of logistics, timing, and co-ordination with other scopes. Each client moving into the business tower requires custom design and built floor plans, adding to the logistics puzzle.
Another was the main ballroom’s piping, which is located three storey’s above the floor level. “That meant the contractor had to use zoom booms to be able to access the ceiling heights,” said Knox.
“A lot of the piping systems in the ceiling were scheduled to be ASJ jacketed fiberglass insulation and wrapped with PVC jacketing, but because of the jacketing on the particular insulation used, we were able to eliminate PVC jacketing in some areas as a cost saving measure.”
The rainwater collection system involves three insulated holding tanks 18×30 feet in diameter and height. “Condensation from within the HVAC system is used to recirculate through the system for heating and cooling,” said Knox.
Low-emissions materials were selected in occupied areas to promote employee health, and thermal energy recycling systems stores cool and warm energy. Overall, the project is designed to perform 30 per cent more efficiently than a traditional building.
At its high point, the project saw 28 insulators on site. As of this writing the job is on time and on budget, with 60 per cent of the insulation scope completed.
The project began in May 2016 and is scheduled for completion in July, 2017.